Leichter bauen und zugleich die Produktivität erhöhen
Für die Inszenierung von Verdis Simone Boccanegra (Regie J.Ph. Gloger, Bühne Ch. Hetzer) legte das Regieteam im Frühjahr 2013 einen Entwurf vor. Drei kastenförmige, auf Stelzen auf der Drehscheibe stehende Spielräume sind so ineinander gebaut, dass Verwandlungen offen und nur durch die Drehung der Scheibe erfolgen. Diese Spielräume (im folgenden als Häuser, rot, blau und grau bezeichnet) werden durch Solisten und Chor mit etwa 100 Personen belastet. Die Drehscheibe hat bei einem Durchmesser von 15 m eine Fläche von 176,62 m² was bei einer zulässigen Tragkraft von 100 kg/m² zu einer maximalen Belastbarkeit von 17,6 t führt. Eine überschlägige Rechnung mit Erfahrungswerten über das Volumen der Dekoration ließ 13 bis 15 t allein für die Dekoration erwarten. Das war einfach zu viel, um noch ca. 100 Personen szenisch mit der Drehscheibe bewegen zu können. Es musste also leichter gebaut werden.
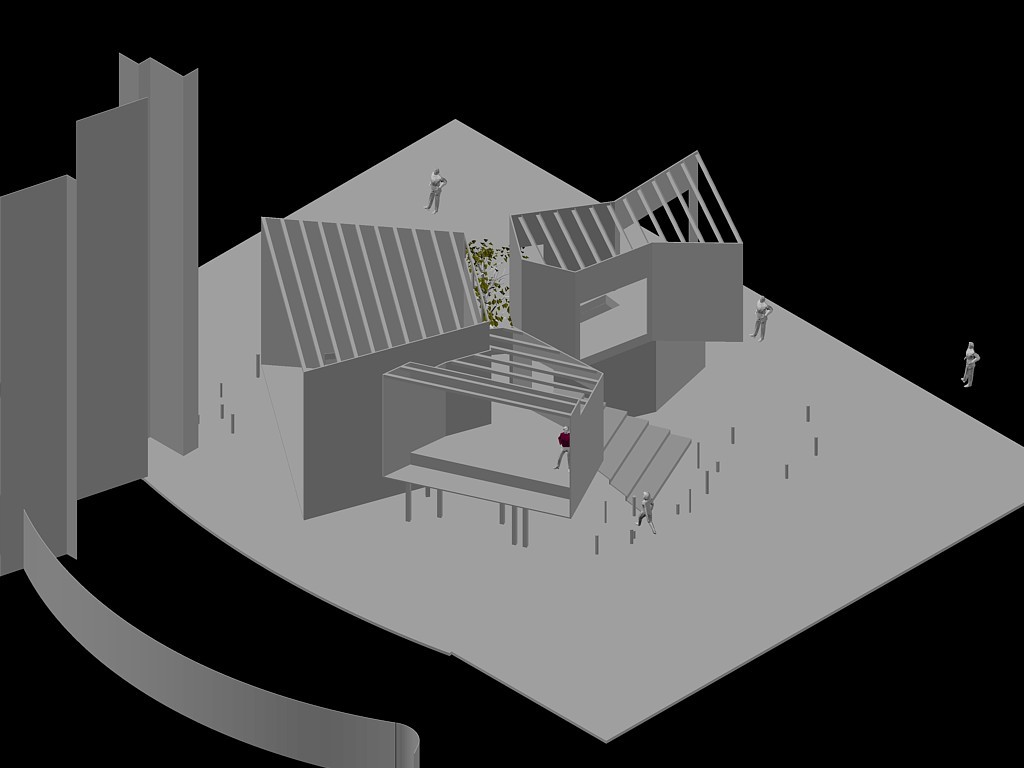
Im Wesentlichen besteht das Bühnenbild aus 3 Kabinetten, die keine geschlossenen Plafonds haben, sondern nach oben durch eine Vielzahl von Balken optisch abgeschlossen sind. Die Spannweite der längsten Balken ist mit über 9 m eine beachtliche Spannweite. Entscheidend für die Durchbiegung dieser Balken ist die statische Höhe sowie die Belastung. Da diese Träger nur durch ihr Eigengewicht belastet werden, ist auch aus diesem Grund ein möglichst geringes Eigengewicht anzustreben.
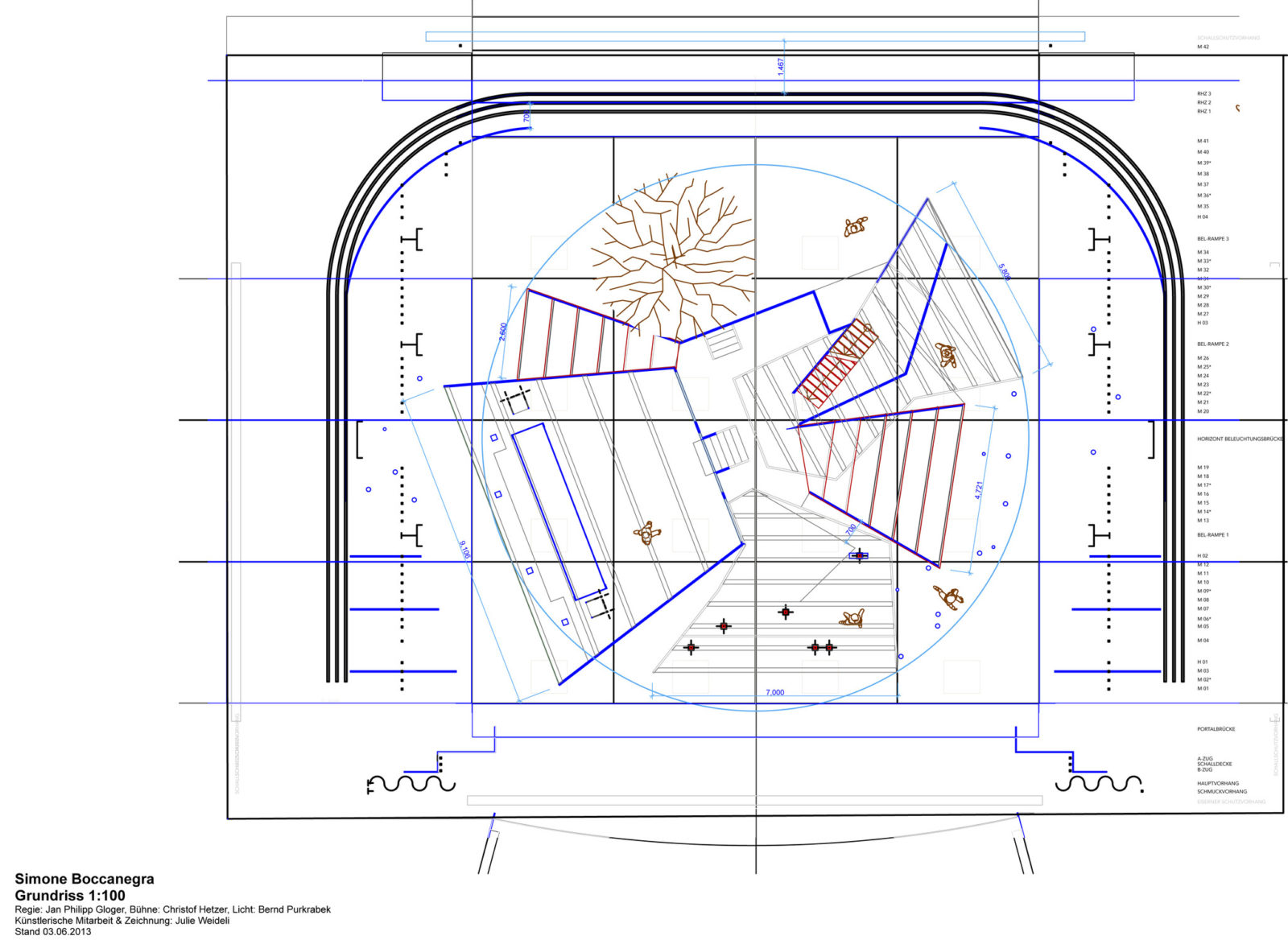
Immer wenn extremer Leichtbau gefragt ist, lohnt sich der Blick nach dem Flugzeugbau. Vieles was dort angewendet wird, ist aufwendige Hightech, die sich nicht so einfach in den handwerklichen Bereich übertragen lässt. Allerdings, wenn man sich in der Geschichte der Luftfahrt umschaut, gibt es Techniken, die durchaus anwendbar sind. So wurden z.B. in den 30er Jahren Segelflugzeuge aus Sperrholz gebaut, wo die Spannten für Rumpf und Flügel aus einer Sperrholzplatte per Hand gesägt wurden, sodass ein Einstückfachwerk entstanden ist. Dieses Konstuktionsprinzip stellt eine elegante Lösung zur Verbindung von Fachwerkstreben dar, da die Traglastfähigkeit von Holzfachwerken in hohem Maße durch die Belastbarkeit der Knotenpunkte bestimmt wird.Ein anderer Bereich, wo ein möglichst geringer Koeffizient aus Masse und Steifigkeit wichtig ist, ist der Bau hochwertiger Lautsprecher. Hier werden die einzelnen Sperrholzplatten nicht per Hand ausgesägt sondern durch moderne CNC-Fräsen.Inspiriert von den Anwendungen, war die Idee geboren, vier Sperrholzplatten über CNC auszufräsen, so dass ein Einstückfachwerk entsteht und vier davon, jeweils eins oben eins unten und eins links und eins rechts zu einer Art Vierpunktträger mittels Dübel undDipl. Ing. Albrecht Löser Leim zu verbinden. Um ein Gefühl zu bekommen, ob das ein gangbarer Weg sein könnte, wurde ein 9m langer Versuchsträger aus 12 mm Birkensperrholz gebaut. Da das verfügbare Sperrholz nur 3050 mm lang ist, musste der Träger aus 3 Teilstücken zusammengesetzt werden.
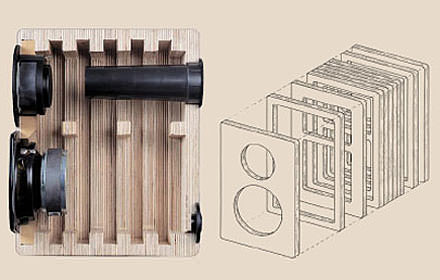
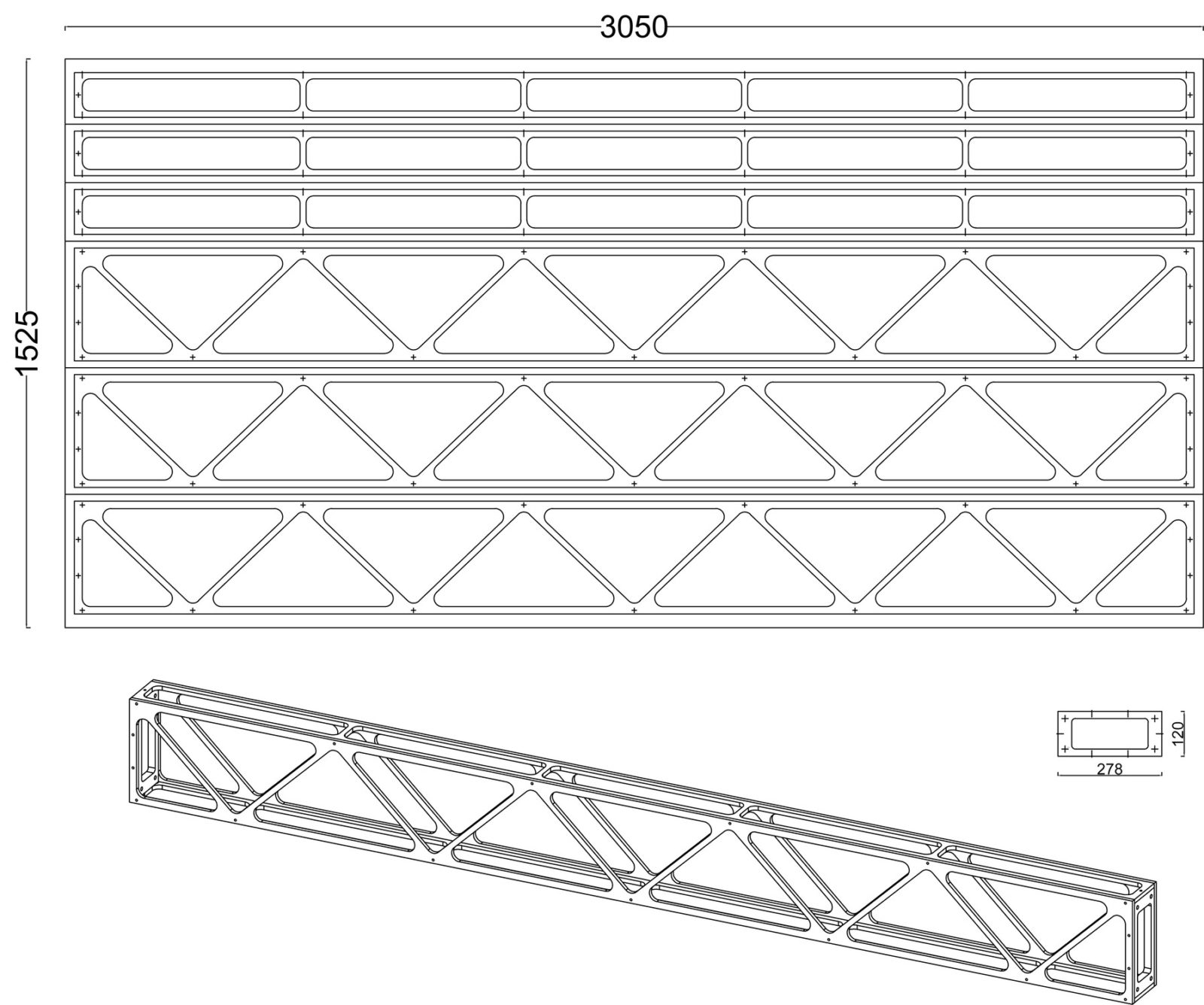
An den Stirnseiten wurde jeweils eine 21 mm starke Sperrholzplatte eingesetzt, die vier Bohrungen enthält, die jeweils mit einer Stahlbuchse ausgekleidet sind (Rampamuffe) so dass die einzelnen Trägerabschnitte über vier M8 Schrauben verbunden werden können (siehe Abb 4,7 und 15).Für den 9m langen Träger sind in Summe
2 Platten 12mm Birkensperrholz BFU CP/C 1,525 m x 3,05 m zum Preis von 92,41 € inkl. Mwst. notwendig. Die Kosten für einen vergleichbaren Träger aus Stahl sind:
5x6m RQ 15×1.5 * 0,99€/m = 29,7€ und 7*6m RQ 20×1.5 * 1,05€/m = 44,1€
Flanschverbindung = 17,77 € in Summe 91,57 € inkl. Mwst.
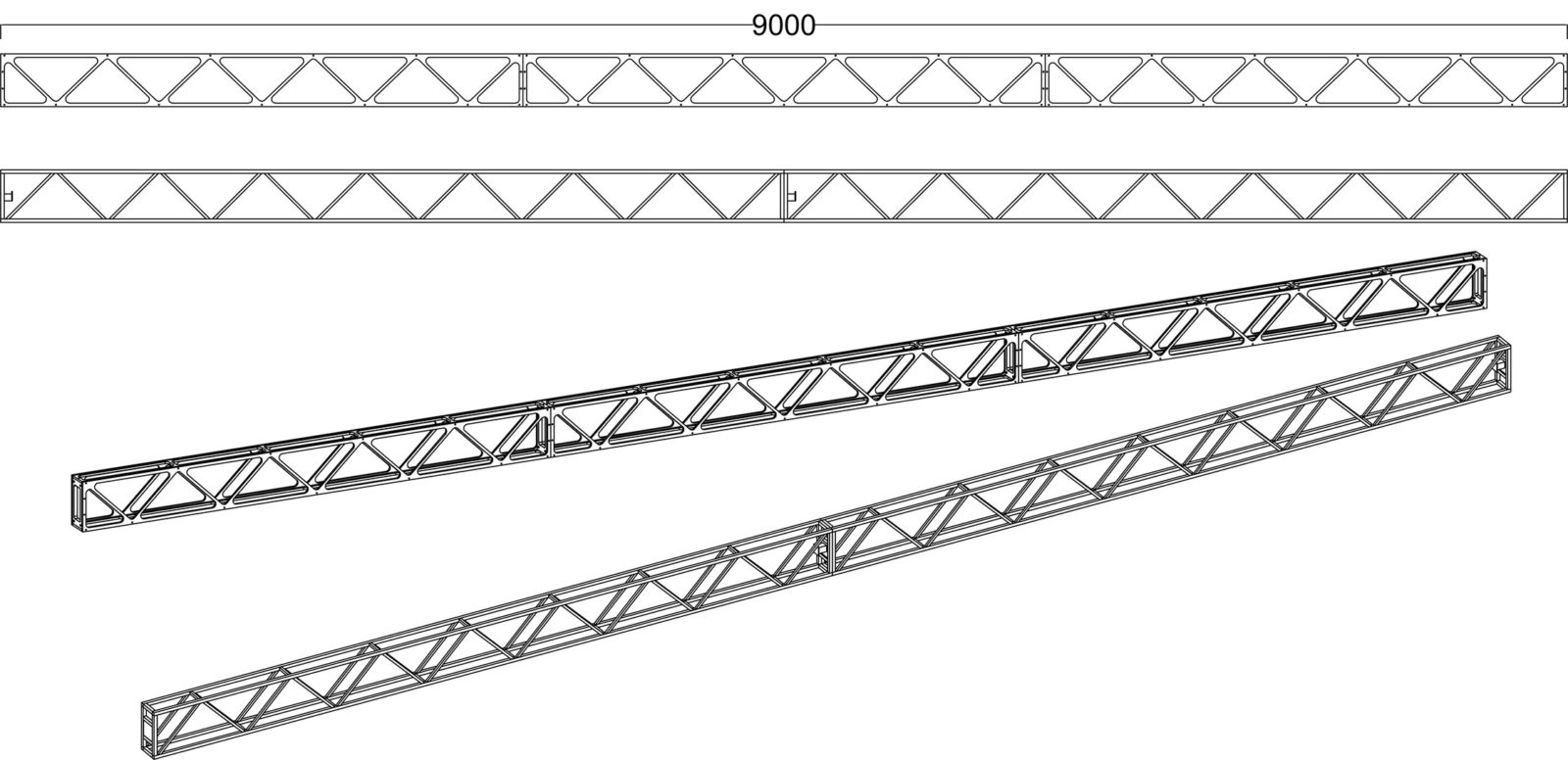
Die reinen Materialkosten sind für beide Träger etwa gleich, wobei der Stahlträger 67kg wiegt, der Träger aus Birkensperrholz aber nur 22 kg! Normalerweise ist Leichtbau mit exponentiell steigenden Kosten verbunden. Wenn es gelingt, die CAD-Daten aus dem am Computer modellierten Modell direkt an die CNC-Fräse zu übergeben, dann ist zusätzlich die Fertigung mit weniger Arbeitsaufwand möglich, somit eine klassische Steigerung der Produktivität durch Automatisierung.
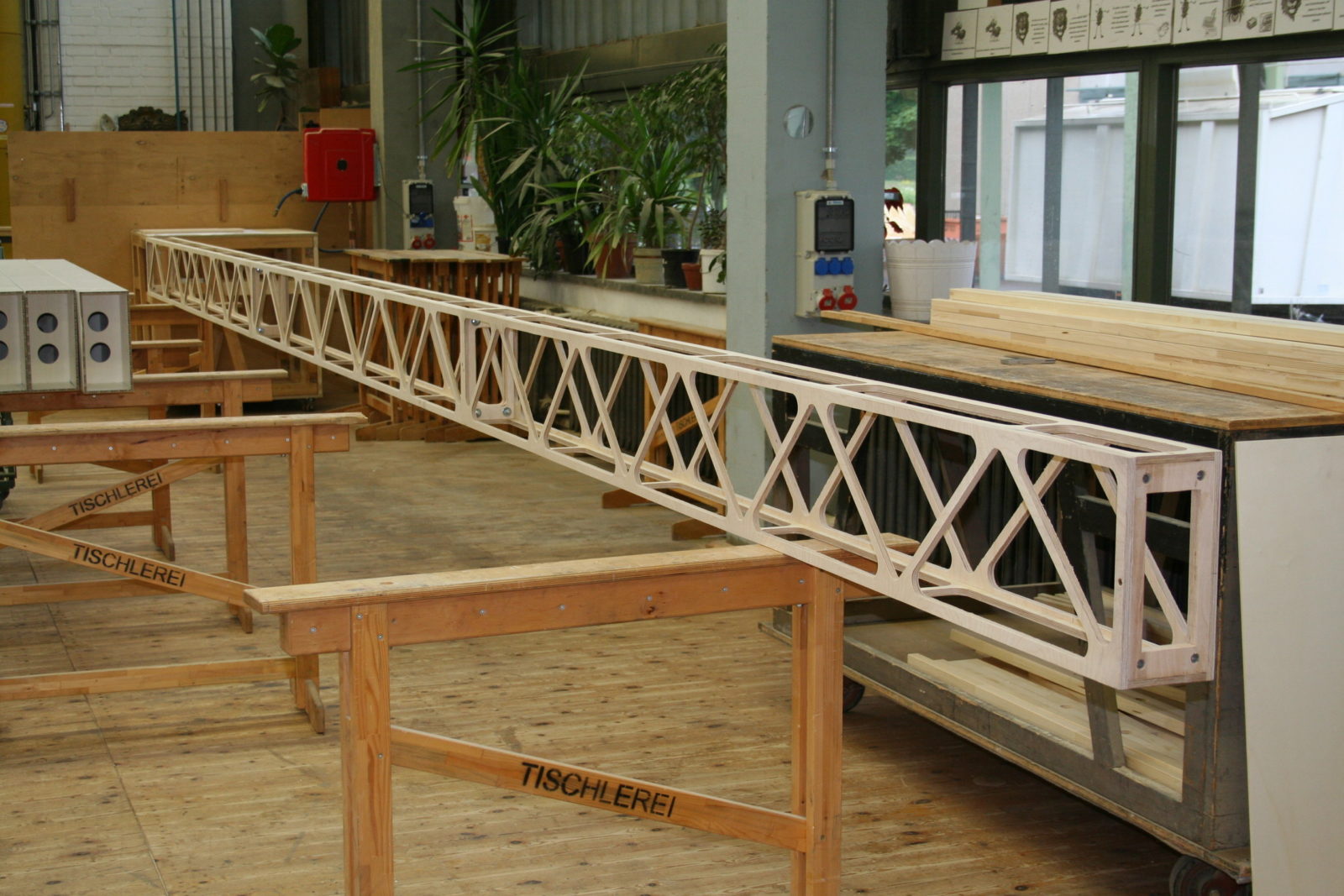
Für einen ersten Versuchsträger wurde die zu fräsende Geometrie als DXF-Daten an die CNC-Fräse übergeben.
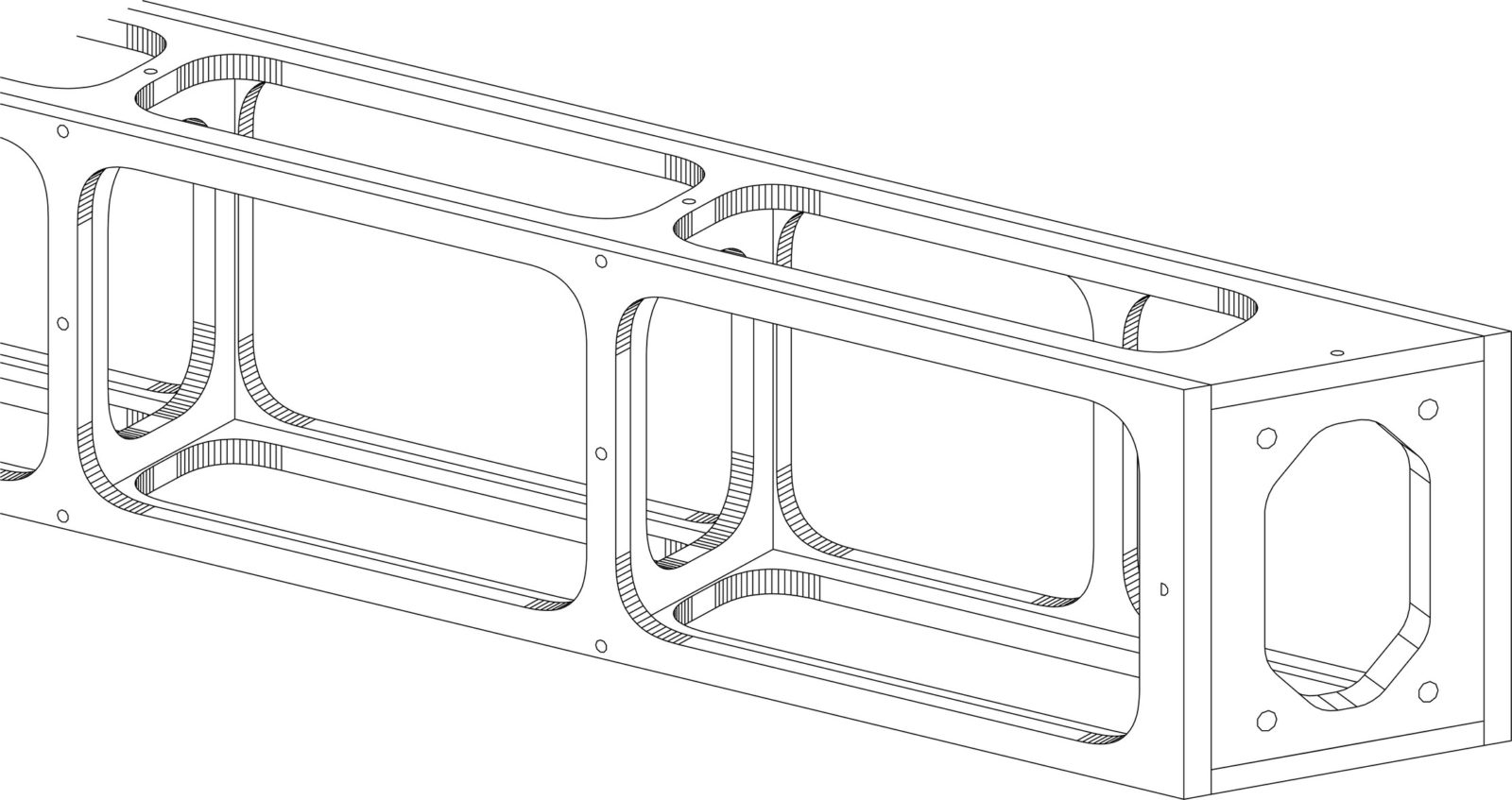
ie mechanischen Eigenschaften eines solchen Trägers wurden durch eine FEM-Analyse überprüft. Die Analyse hat ergeben, dass für die großen Spannweiten von 9 m eine Ausfachung mit Diagonalen sinnvoll ist, um die Durchbiegung gering zu halten. Bei Trägern unter 6 m Spannweite und den Säulen, lässt sich auf das Konstruktionsprinzip Viereendelträger zurückgreifen, was es ermöglicht, an den Senkrechten jeweils ein ebenfalls ausgefrästes Schott zu platzieren, was die Torsionssteifigkeit und Beschädigung beim Transport senkrecht zur Plattenebene deutlich verringern dürfte. Auch ist die Modellierung im CAD einfacher.
Für die „abgerundeten Ecken“ wurden in einem ersten Schritt Kreisbögen mit einem Radius von 20 mm verwendet. Um die „Sollbruchstelle“ am Übergang zwischen linear und radial etwas abzumildern, wurde zum Vergleich mit einem Übergangsbogen (Klothide), bei dem der Radius linear auf 20 mm in 45° ansteigt und dann wieder linear fällt, gerechnet. Die Vergleichsrechnung hat ergeben, dass bei einem 6m langen Träger die Durchbiegung unter Eigenlast mit 20 mm Radius Abrundung in den Ecken 6,1 mm ist. Der gleiche Träger mit einem Übergangsbogen und ansonsten gleichen Randbedingungen nur eine Durchbiegung von 5,3 mm hat. Das bedeutet etwa 20% mehr Steifigkeit bei vernachlässigbarer Gewichtszunahme.
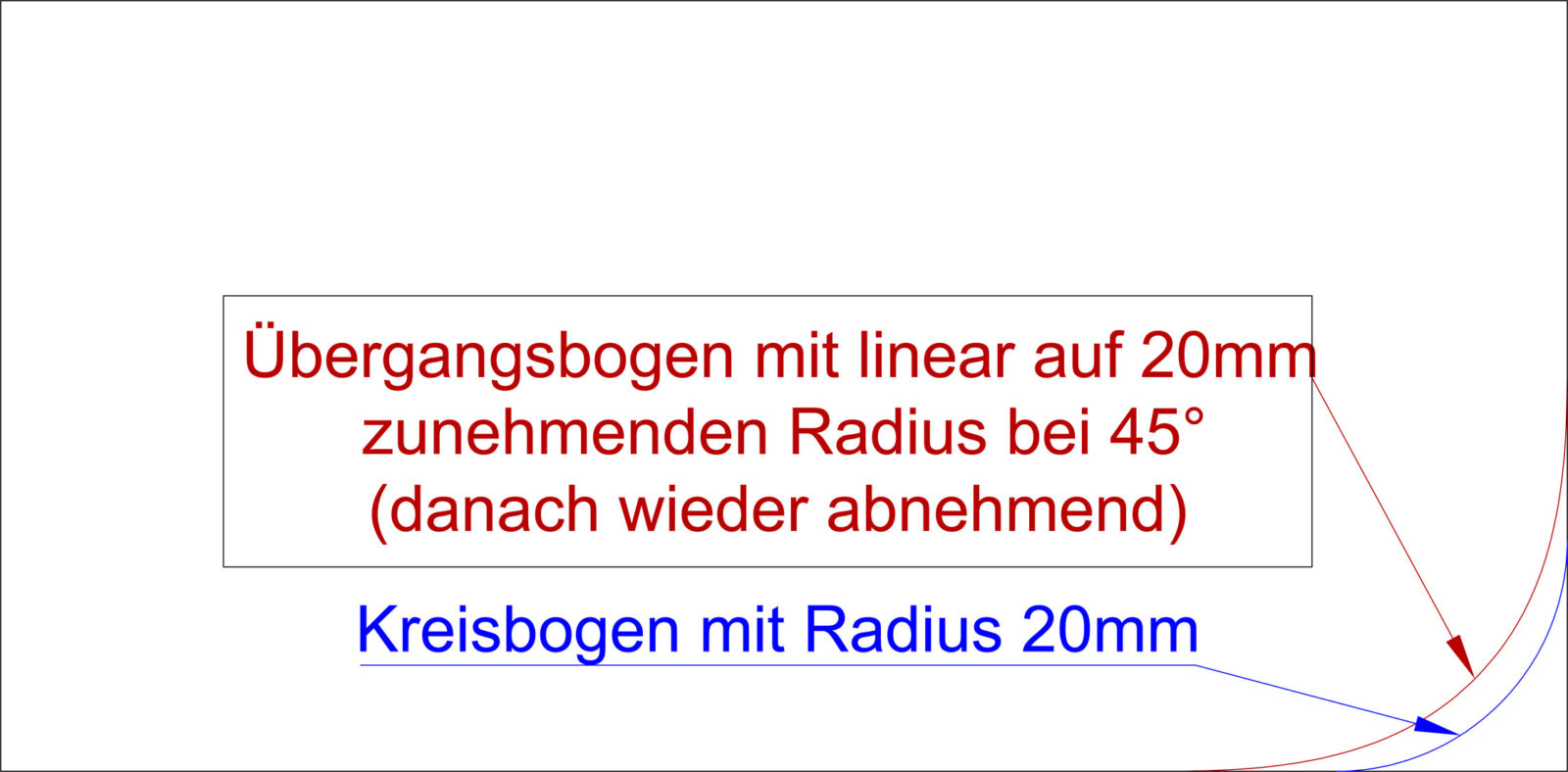
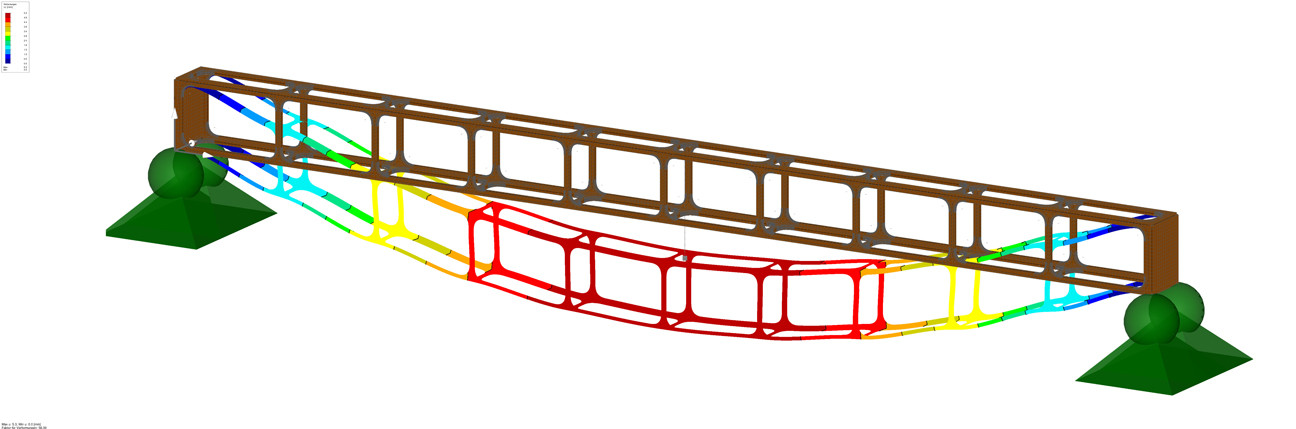
Durch die Vielzahl von verschiedenen Trägern und Stützen, die für die 3 Häuser notwendig sind, war es sehr wünschenswert, die Daten für die Vielzahl der verschiedenen Platten aus dem CAD-Programm direkter als über das DXF-Format an die CNC-Fräse zu übergeben. Die Firma CAMid GmbH in Frangart (Südtirol) ist über ihre selbst programmierte Schnittstelle in der Lage, so ziemlich alle CNC gesteuerten Fräs-und Schneidmaschinen anzusteuern. Nach Überwindung anfänglicher Schwierigkeiten war es möglich, die CAD-Daten so zu exportieren, dass die Firma CAMid mit Hilfe ihrer Schnittstelle für jede benötigte Platte ein Programm ausgeben konnte, was die Firma Ligneus (Ottendorf-Okrilla) an ihrer HOMAG-CNC-Fräse starten konnte. Dieser Prozess lässt sich sicherlich optimieren, wenn Modellierung und Fräsung in einer Hand liegen.
Bis hierher ging es um Träger, die im Wesentlichen nur ihre Eigenlast tragen müssen. Für Träger die mit einer Verkehrslast belastet werden, müssen die Flanken der Träger mit Sicherheit verstärkt werden. Hierfür bietet sich die klassische Form des Doppel-T-Trägers an. Allerdings wäre in den Flanken klassisches Sperrholz suboptimal, da Holz quer zur Faser wesentlich weniger belastet werden kann als in Faserrichtung, deshalb wurde für die Flanken auf Lagenholz zurückgegriffen. Lagenholz besteht genau wie Sperrholz aus dünnen Furnierschichten nur mit dem Unterschied, dass alle Schichten die gleiche Faserrichtung haben. Da für diese konstruktive Anwendung keine flächige Lastabtragung stattfindet, überwiegen die Vorteile des Lagenholzes gegenüber Sperrholz bei weitem. Lagenholz ist auch weit mehr homogenisiert als Brettschichtholz, deshalb sind die zulässigen Spannungen im Lagenholz höher und sind, wenn dies statisch erforderlich ist, dem Brettschichtholz vorzuziehen.
A=1062 mm² (Holzquerschnitt) zul. Spannung 50 N/mm = zul. Normalkraft 53,1 kN
A=216 mm² (Stahlquerschnitt RR 50x25x1.5) zul. Spannung 214 N/mm² = zul. Normalkraft 46,2 kN
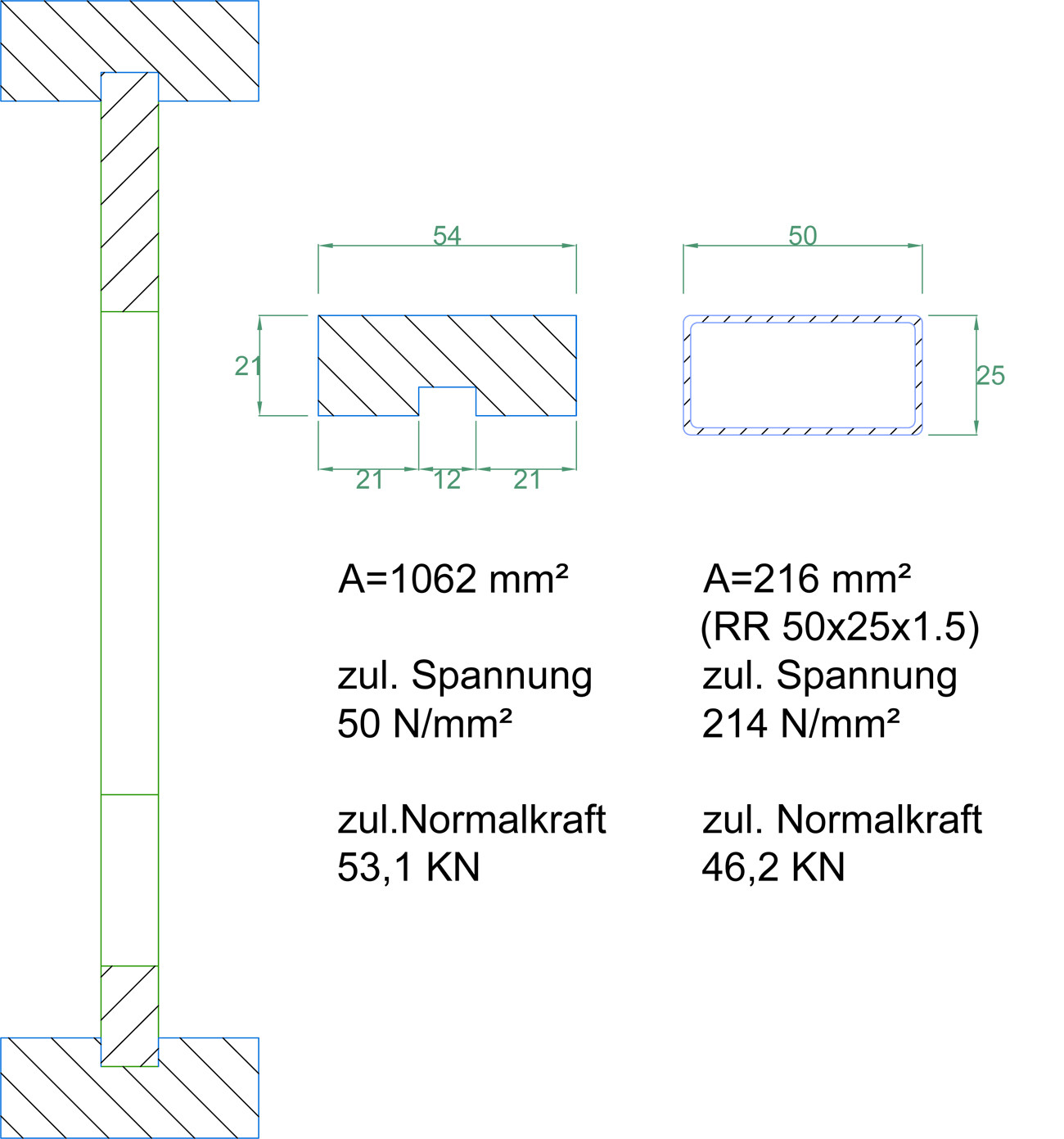
Lagenholz wird als Endlosband produziert. Begrenzung in der Länge ist also nur das Transportmaß. Es können durchaus lange Teile von 7 bis 9 m ohne Stoß produziert werden. Für die Konstruktion der Träger der begehbaren Bodenplatte wurde ein Streifen Lagenholz in etwa der Dimension eines Stahlprofils RR 50x25x1.5 gewählt, welches sonst an dieser Stelle verwendet worden wäre. Das besagte Stahlprofil wiegt etwa 1,7 kg/m während das Profil aus Lagenholz mit 0,51 kg/m deutlich leichter ist. Ein Vergleich der zulässigen Normalkraft kann als Indiz für die Belastbarkeit dienen. Hier schneidet das Lagenholz mit weniger als ein Drittel der Masse besser ab als das Stahlprofil.
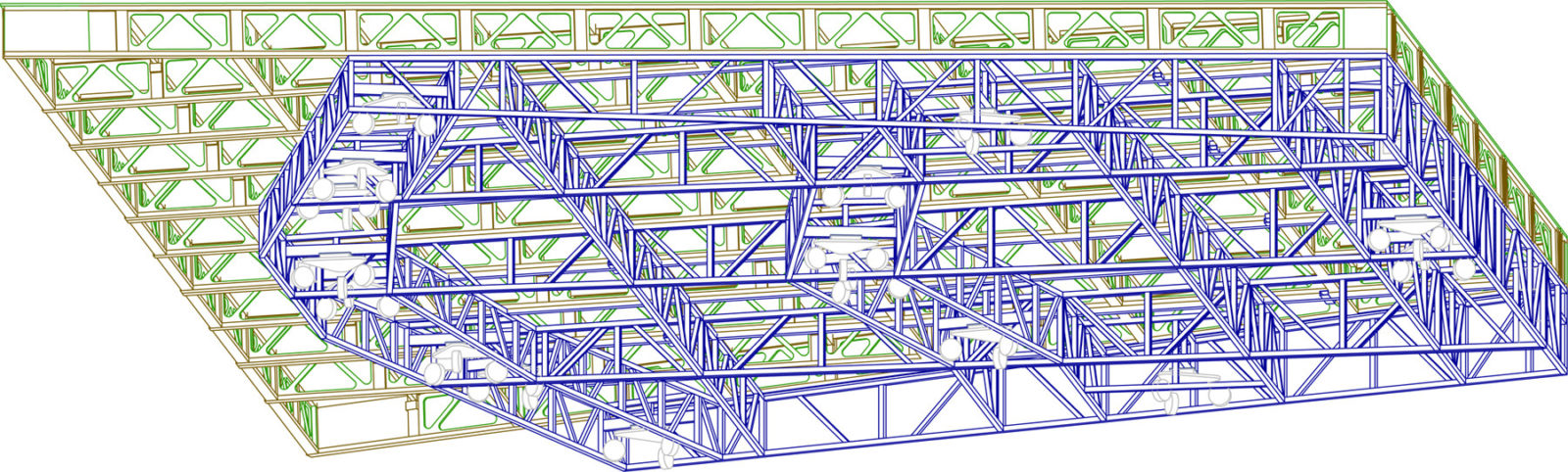
Unterkonstruktion des roten Hauses von schräg unten gesehen, mit einem Stahlwagen und der Plattform aus Holz, die etwa 1,5m auskragt. Auch dieser Doppel-T-Träger wurde in RFEM auf seine Tragfähigkeit hin überprüft, da er mit einer maximalen Dichte von etwa 40 Choristen bespielt werden sollte. Die Tragfähigkeit konnte problemlos nachgewiesen werden. Auch hier zeigt sich, dass durch den sinnvollen Einsatz von Holzwerkstoffen Gewicht gespart werden kann.
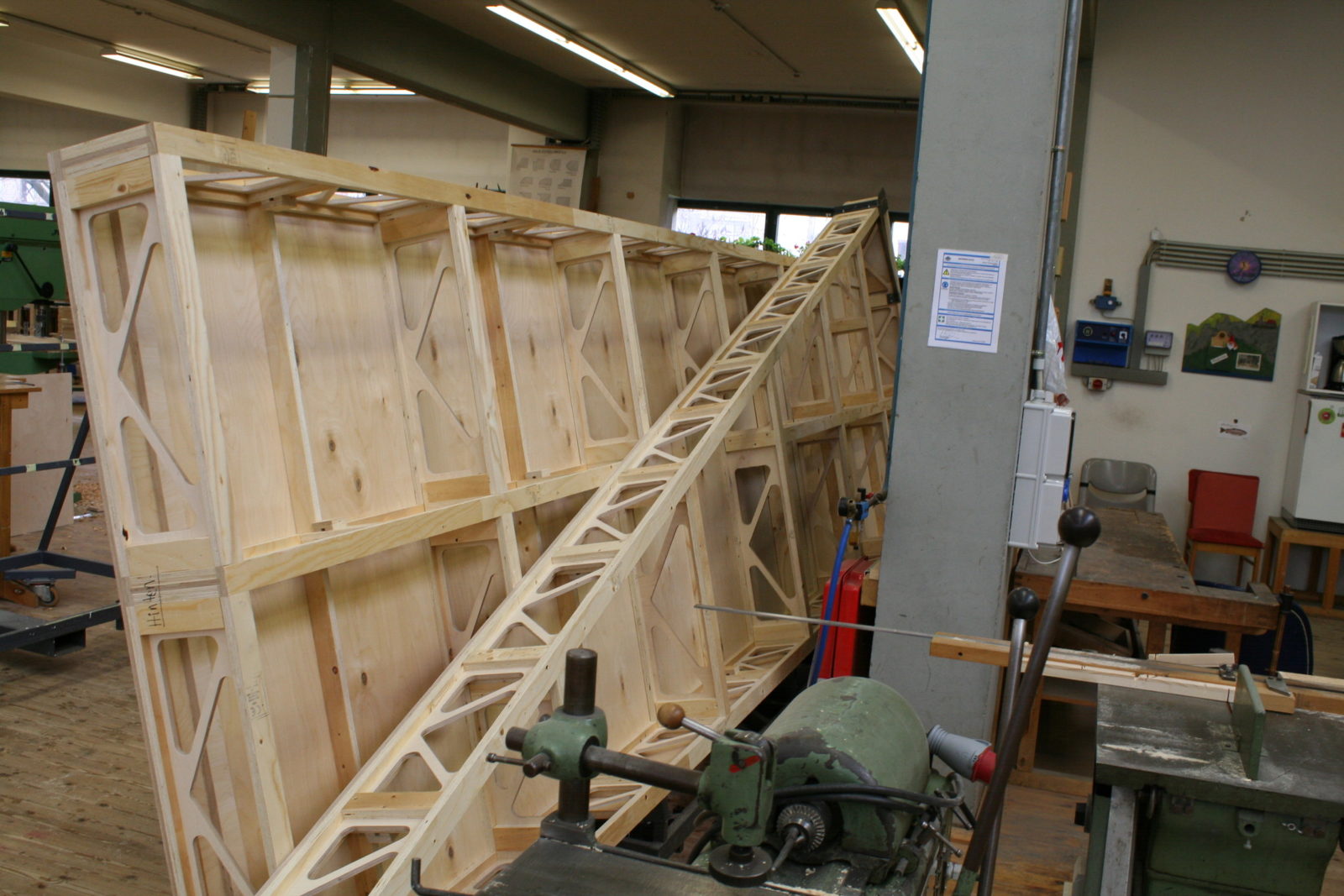
Mit Hilfe dieses Lagenholzes lässt sich auch der eingangs beschriebene Vierpunktträger so bauen, dass er höheren statischen Belastungen stand hält und nicht nur für das Eigengewicht optimiert ist.Ein weiterer Schritt zur Gewichtseinsparung war, die sichtbaren Flächen durch Stoffbespannungen zu ersetzen. An den Innenseiten des grauen und roten Raumes war dies aus optischen und akustischen Gründen nicht möglich. Hier wurde auf sogenanntes Flugzeugsperrholz (Feinschichtsperrholz) von 2,5 mm Stärke bei 5 Lagen zurückgegriffen.
Als Aussteifung und Tragkonstruktion für die Verkleidung wurde nicht die sonst übliche Brettschichtholzlatte (Theaterlatte) von 60×28 mm verwendet, sondern 10 mm dicke Streifen aus Birkensperrholz, die durch Schlitzungen bis zur Mitte an Kreuzungspunkten ineinander gesteckt werden und durch Bohrungen von 50 mm Durchmesser in den Bereichen, wo das Material aus statischen Gründen nicht gebraucht wird, abgemagert werden. Somit war eine relativ große statische Höhe der Tragkonstruktion für die Verkleidung möglich und die Anzahl der Stützen, an denen die Verkleidung befestigt werden muss, konnte dadurch reduziert werden.

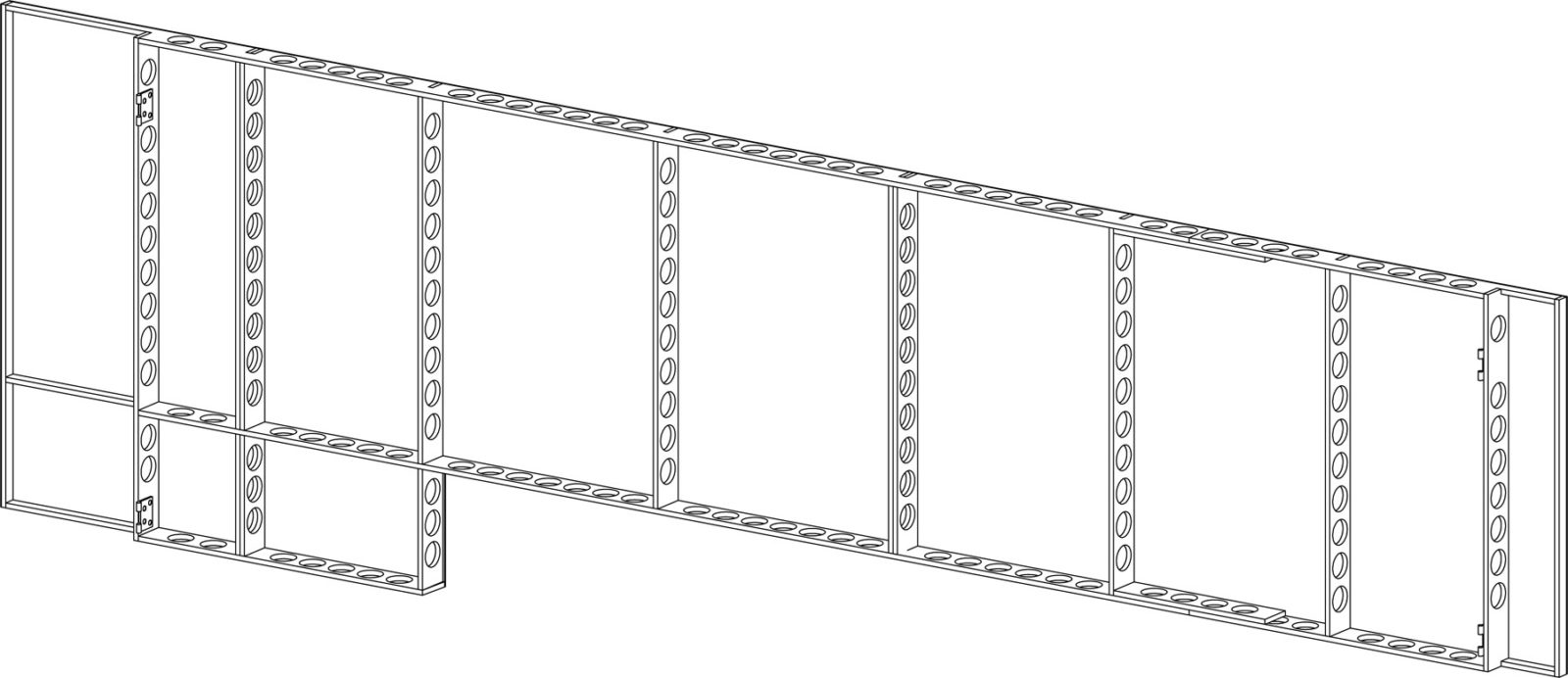
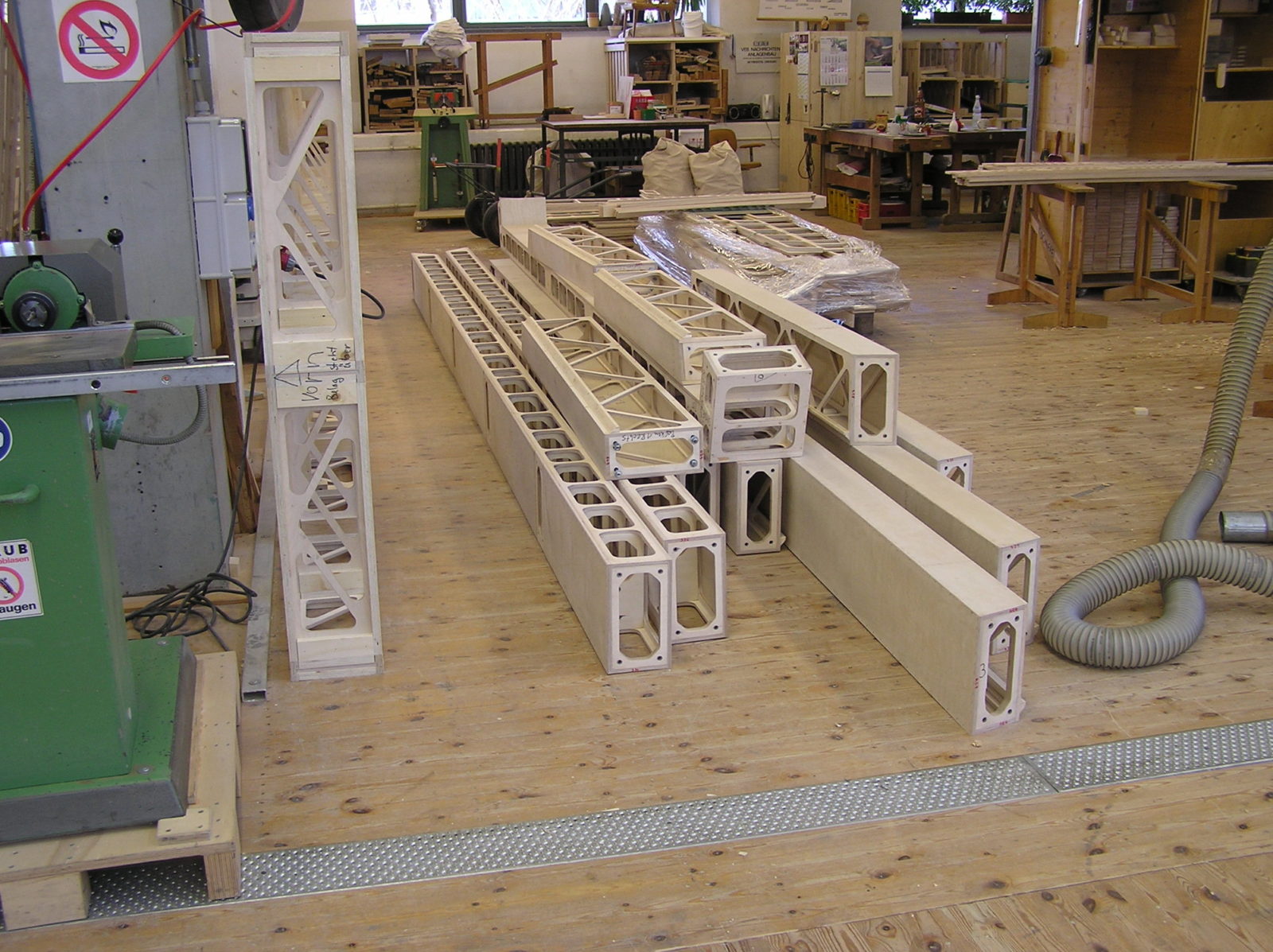
Die Fertigung ist an den Theaterwerkstätten der Semperoper erfolgt und wurde von der Konstruktionsabteilung begleitet. Zu Beginn war es für alle Beteiligten Neuland und auch zeitintensiv. Allerdings hat sich dann ein praktikabler Fertigungsablauf in den Werkstätten herauskristallisiert, so dass die Fertigung sehr sehr zügig von statten ging.
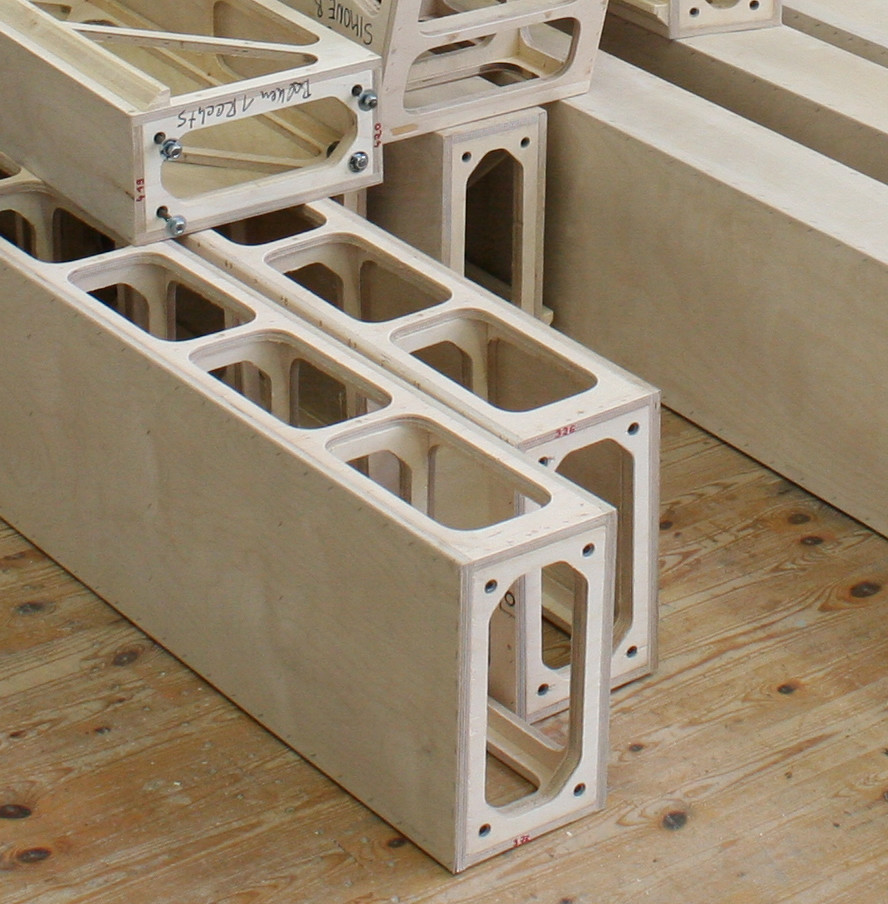
In dem CAD-Modell wurden alle Dübellöcher auch die Senkbohrungen in die Stirnseiten der Platten modelliert. Diese waagerechten Bohrungen machten die Fräsung für die Firma LIGNEUS aufwendig und waren nicht besonders hilfreich bei der Fertigung. Darauf sollte in der Zukunft verzichtet werden. Die Bohrungen senkrecht zur Platte wirken wie eine Bohrlehre mit der sich die Bohrungen in die Stirnseite schnell per Hand bei der Montage machen lassen. Auch die schrägen Kanten an den abgewinkelten Säulen sind schneller und präziser auf einer klassischen Abrichte gemacht. Das bedeutet, dass im Prinzip nur eine ganz einfache 2D-CNC-Fräse, die nur senkrecht zum Arbeitstisch arbeiten kann, ausreicht, die allerdings mit einem möglichst großen Arbeitstisch.
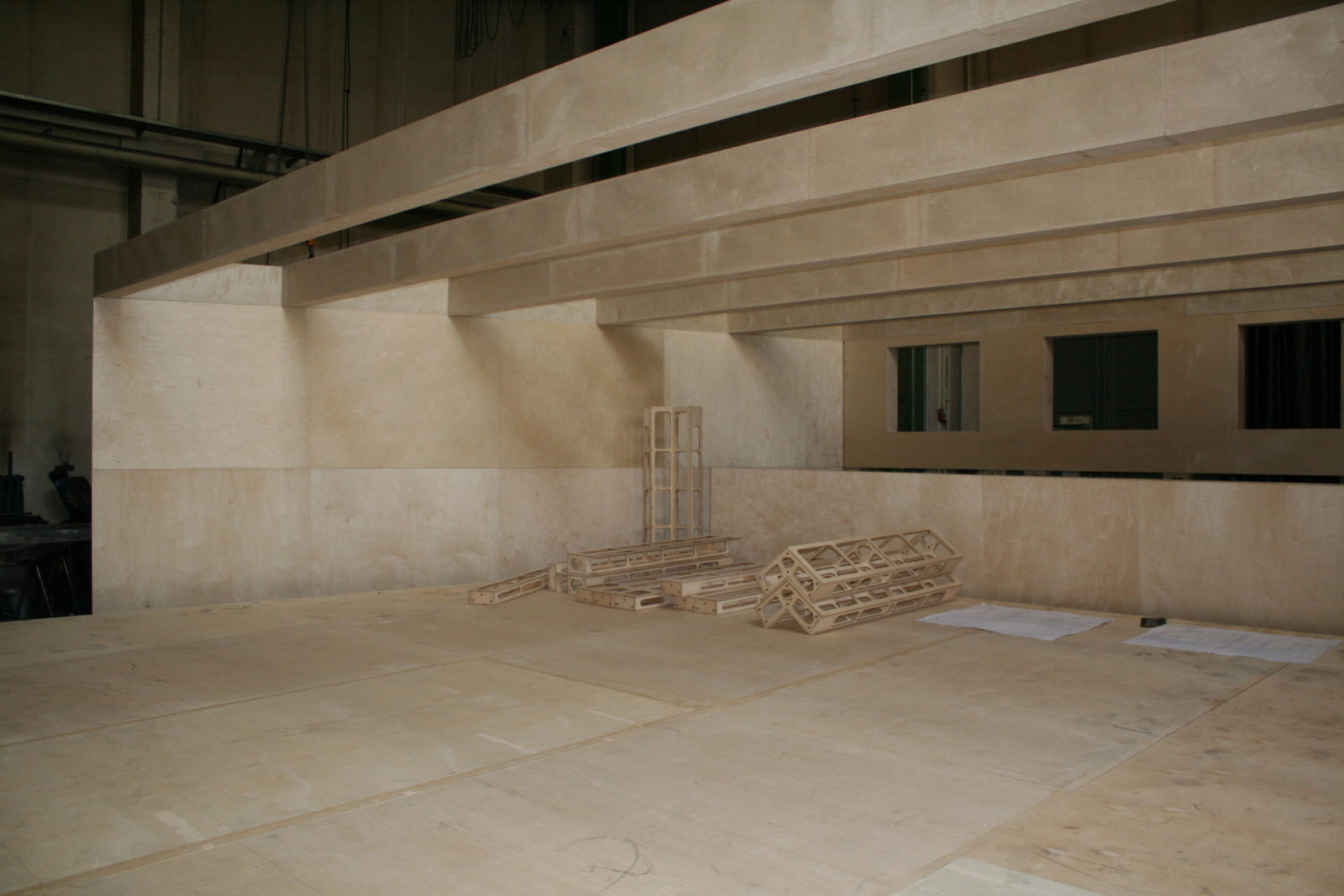
Die eingeschraubten Stahlbuchsen waren handelsübliche Rampamuffen. Sicherlich wäre es hier vorteilhaft, eine Spezialmuffe zu haben, die eine Krempe hat, so dass bei der Montage auf der Bühne auf die Unterlegscheibe verzichtet werden kann. Bei entsprechenden Stückzahlen muss diese Muffe nicht teurer sein als die verwendete.Das Gesamtgewicht der Dekoration hat der Computer nach der kompletten Modellierung im CAD, inklusive 20% Aufschlag für Kleinteile und Farbe etc., mit 6,6 t berechnet. Das entspricht ca. der Hälfte von 13 bis 15 t bei konventioneller Bauweise (s. Einleitung).
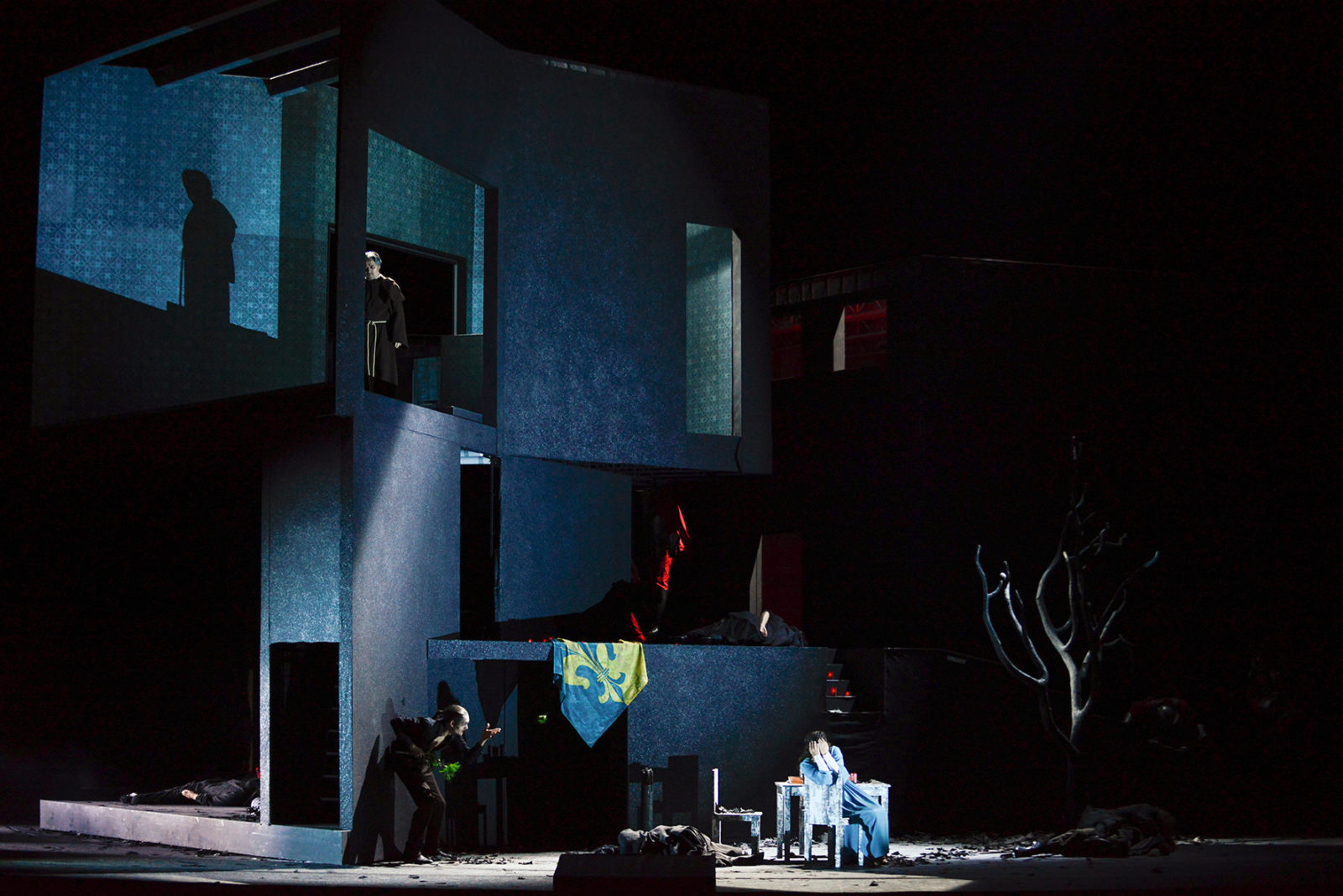
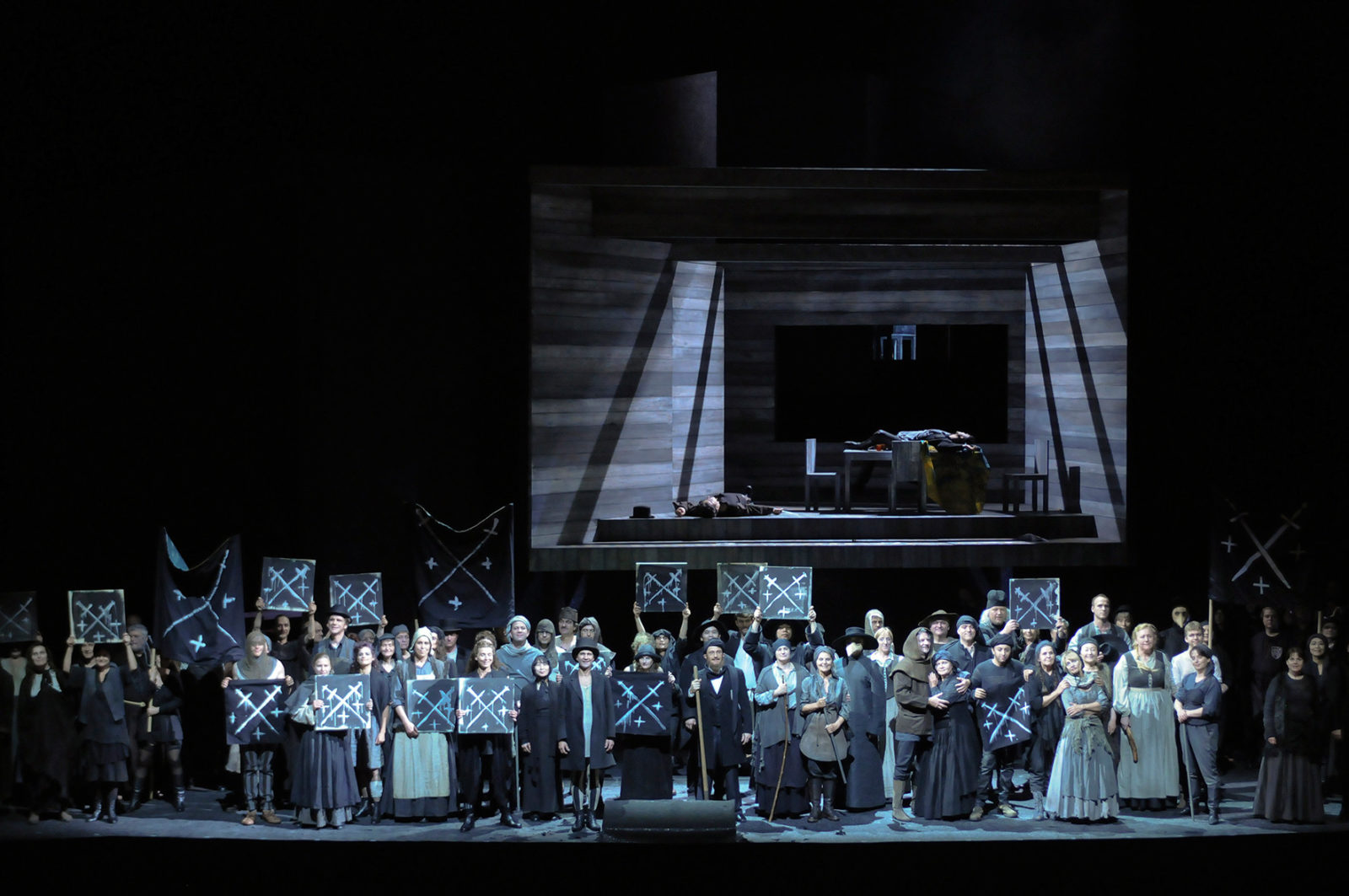
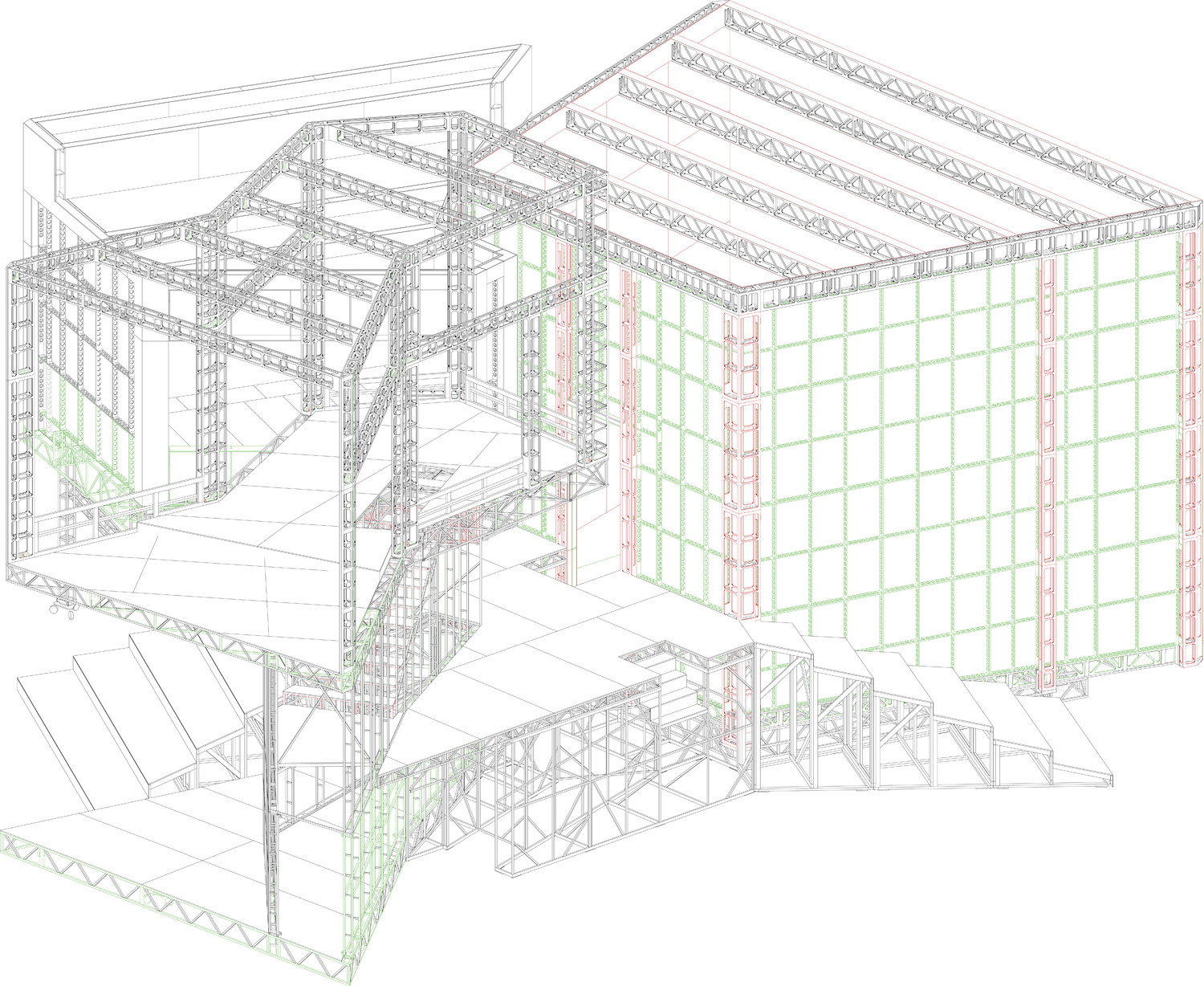